Sodium Permanganate Well Injection
- toddwhanna
- Aug 13, 2024
- 2 min read
Updated: Aug 14, 2024
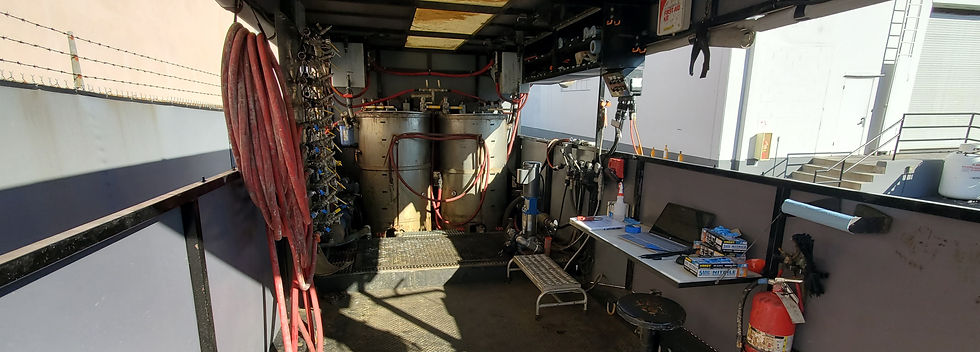
This was not our standard Sodium Permanganate injection project. The Legacy team was contracted by a local engineering firm that recently took this project over from another consultant, who had been self-implementing ISCO injections at a project site in Los Angeles County. The goal was to use the ~7,000 gallons of 40% Sodium Permanganate that was currently stored onsite, dilute it down to a 10% concentration, and inject it into eight (8) existing 2-inch PVC Injection Wells.

Pre-project site visits aren't always necessary, but it this case it was very important.
This image was taken inside the onsite treatment compound that contained both Soil Vapor and Groundwater Treatment Systems.
Also within this compound area, there were three Poly Storage Tanks that ranged in size from 2k to 6k gallons. Combined these tanks contained ~7,000 gallons of 40% Sodium Permanganate.
For those of us who handle and work with chemicals and remediation compounds daily, this looks like a Crime Scene. This single image says so much about Inexperience, Chemical Incompatibility, Safety and Housekeeping to name a few.

The first step was to do some general clean-up and neutralization of the Sodium Permanganate that seemed to be everywhere.
We used our standard neutralization mixture containing Hydrogen Peroxide, Acid and Water.
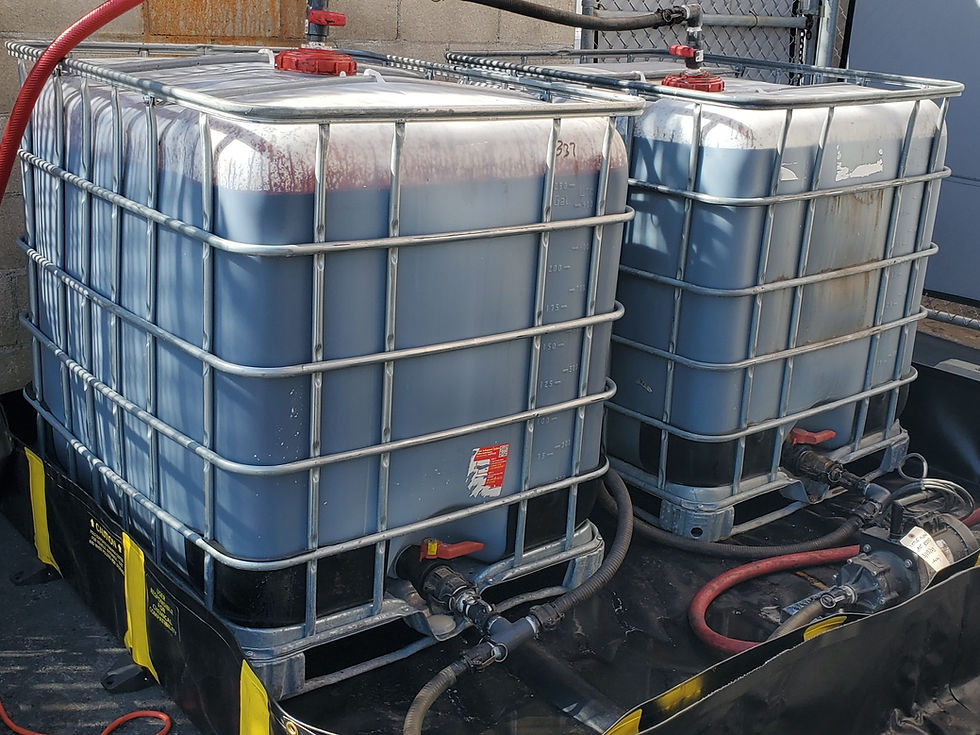
The next step was to start pull the 40% Sodium Permanganate liquid out of the onsite vertical tanks.
We used two (2) IBC totes that allowed us to accurately track the amount of Sodium Permanganate used.

We mixed the Sodium Permanganate, pumped, and monitored the injection process from one of our self-contained Injection Trailer.

We had some theft issues with the Hydrant Meter and Backflow Device.
One day it was there locked to the meter.
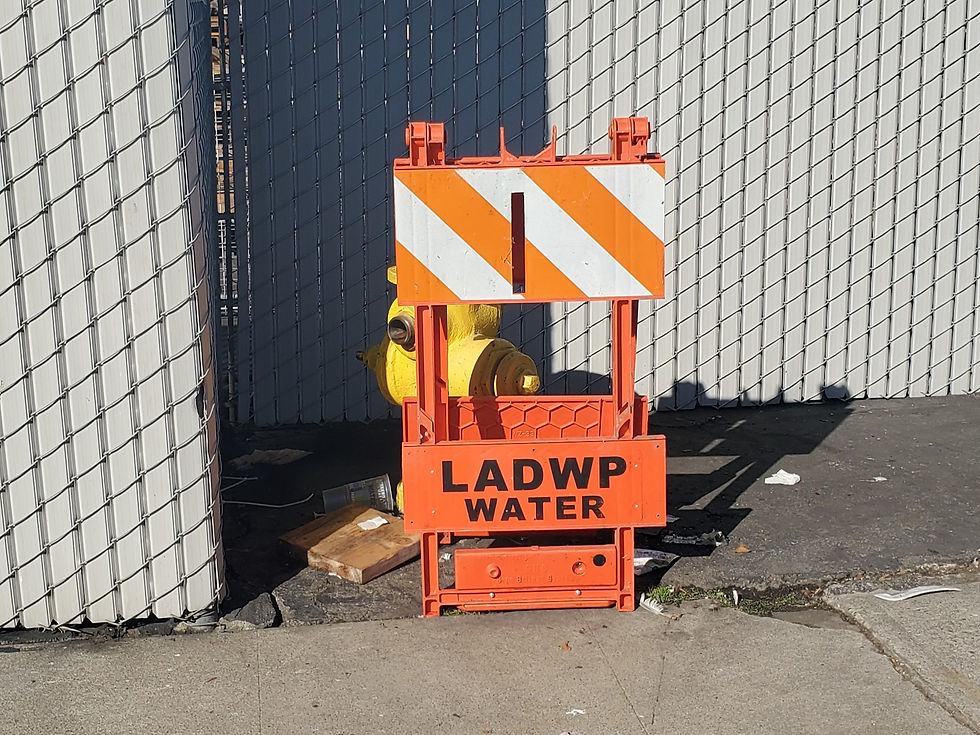
The next day it wasn't
Luckily LADWP was able to bring us a new one within a few hours.

The 2-inch Injection Wells were connected to lateral piping from the treatment area, however the lateral piping was compromised, so we were unable to use it.
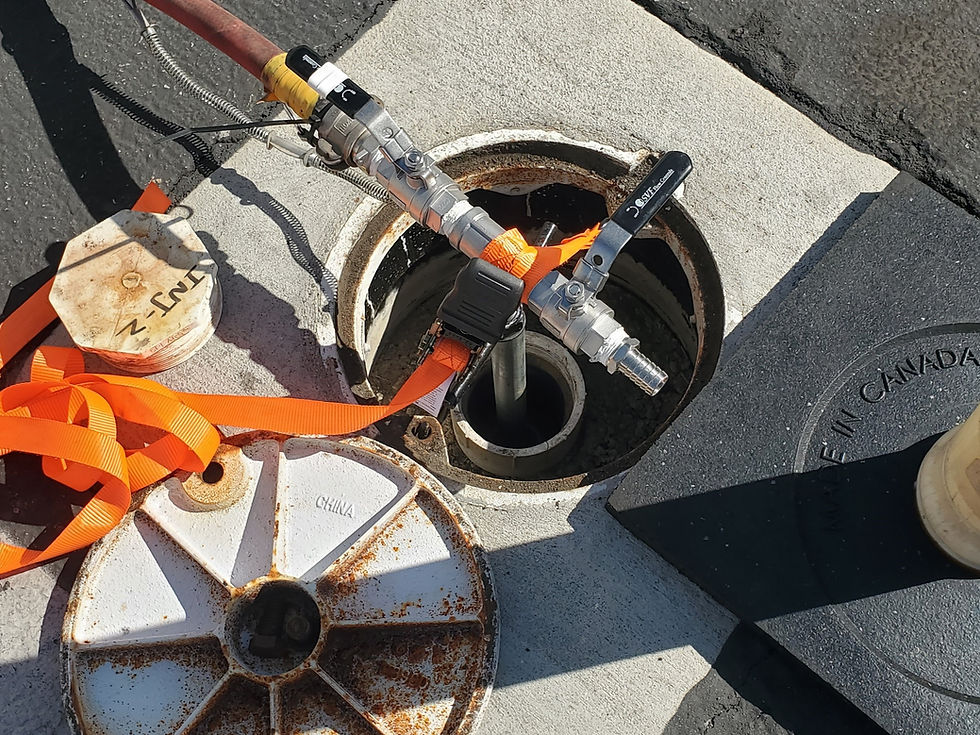
To avoid the ISCO reagent from getting into the lateral piping, we used mechanical packers that sealed within the well casing below the lateral supply fitting.
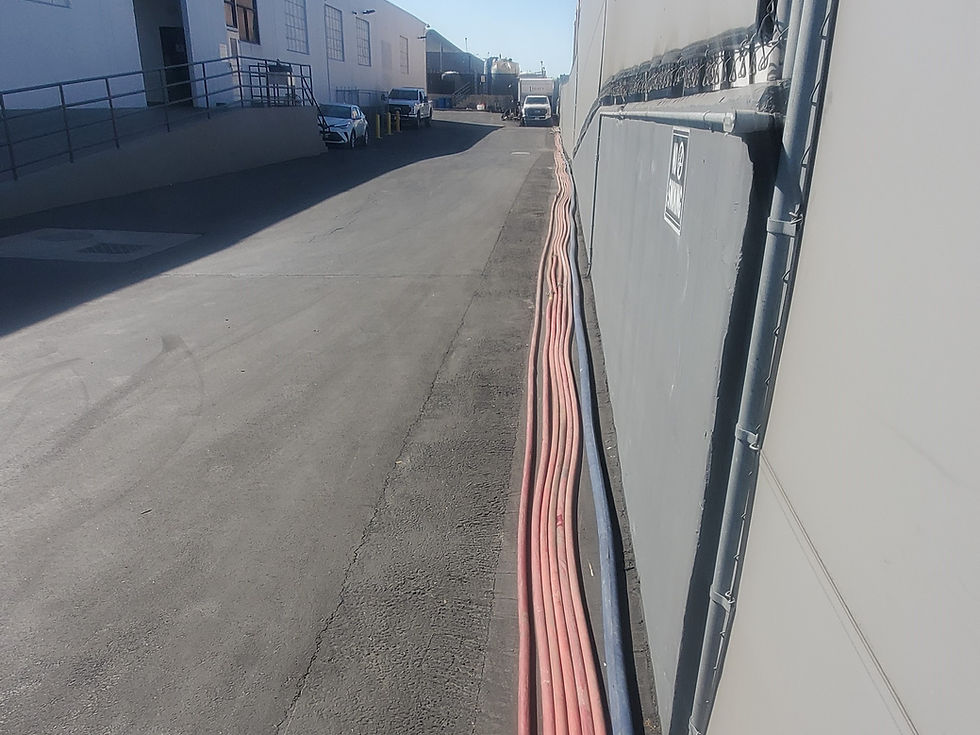
We had long 300-500 foot injection hose runs going to the Injection Wells.
The field crew did a good job at keeping the lines neat and tidy as usual.

Some of the off-site wells were located near a homeless RV encampment.
We did our best to keep the public at a safe distance from our field efforts.

We injected into all eight wells simultaneously, with the use of our 10-Point Injection Manifold.
Our Injection Manifold is fitted with individual pressure gauges and digital Ultrasonic Flowmeters / Totalizers. This allows our our field crews to accurately deliver the prescribed amount of oxidant, within the design specifications.
Once the Well Injection was completed, we assisted our client with the clean-up and neutralization of the treatment compound and equipment, as well as triple rinsing of the three (3) vertical Poly Tanks.

This post can also be viewed on our LinkedIn page. Follow Legacy Remediation on LinkedIn to stay up to date with all the things we are up to.
If you have any questions on this project, or if we can help support any of your current or upcoming projects, please contact us.